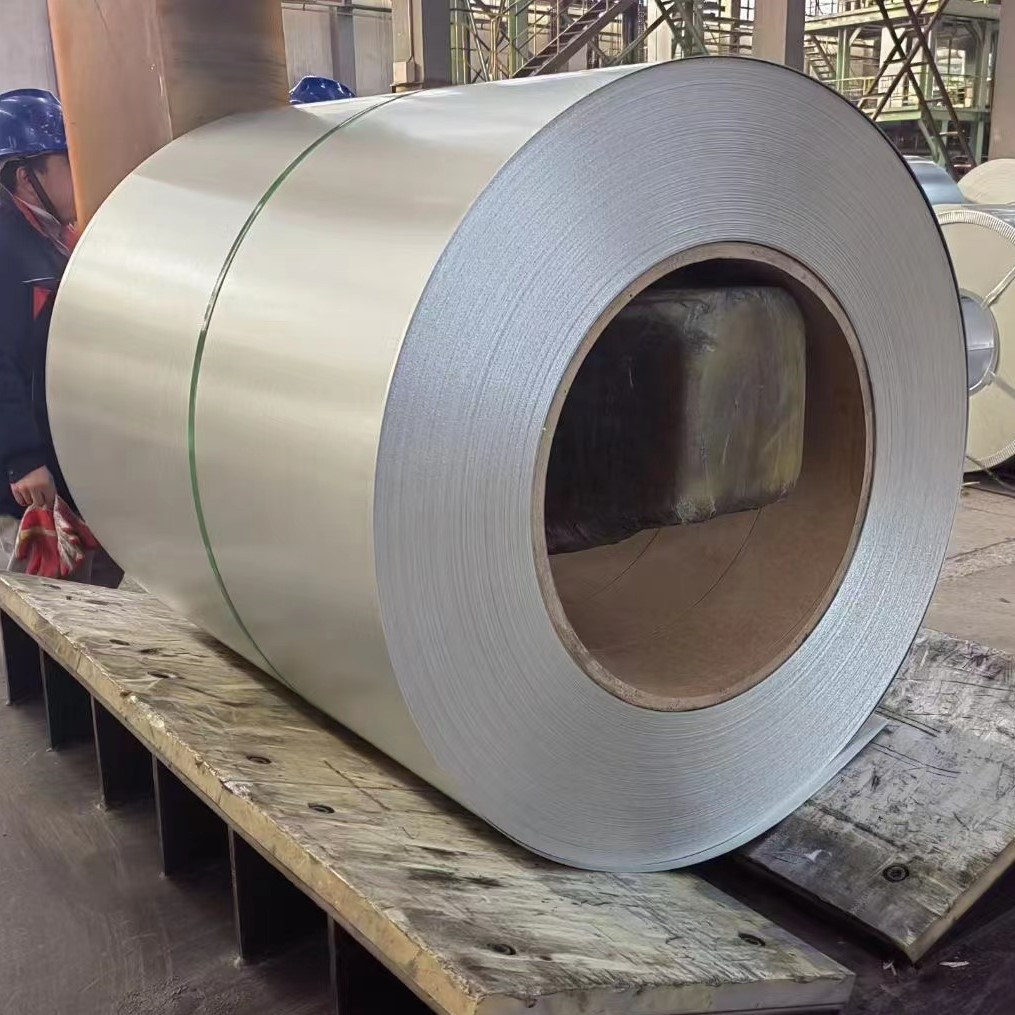
Aluzinc coated steel and stainless steel are both highly regarded materials in various industrial and architectural applications. While both materials offer excellent corrosion resistance, they differ significantly in composition, properties, processing methods, and applications. Understanding these differences is crucial for selecting the right material for specific uses, as each offers distinct advantages depending on the environmental and performance requirements.
1. Composition and Structure
The primary difference between aluzinc coated steel and stainless steel lies in their composition. Stainless steel consists mainly of iron, chromium, and nickel, with chromium content typically exceeding 10.5%. The chromium in stainless steel forms a dense, passive oxide layer that provides its exceptional corrosion resistance. On the other hand, aluzinc coated steel is created by applying a coating of aluminum, zinc, and a small amount of silicon to the surface of steel. In this composite, aluminum offers oxidation resistance and cathodic protection, while zinc acts as a sacrificial anode to protect the steel from corrosion. Silicon improves the adhesion between the coating and the base steel.
2. Corrosion Resistance
Both aluzinc coated steel and stainless steel are known for their excellent corrosion resistance, but their performance in different environments can vary. Stainless steel, particularly high-nickel austenitic grades like 316, offers superior resistance in harsh environments, including acidic, alkaline, and chlorinated conditions. It can withstand exposure to seawater and industrial pollutants. However, in extreme conditions with high salt, acid, or humidity, stainless steel may still corrode.
Aluzinc coated steel, while also highly resistant to corrosion, performs best in atmospheric environments, particularly in industrial or coastal regions. The aluminum-zinc alloy coating forms an oxide layer that effectively protects the material from moisture and air. In many applications, aluzinc coated steel’s corrosion resistance rivals that of stainless steel, especially in environments where the material is exposed to industrial pollutants or marine climates. However, in highly acidic or alkaline environments, aluzinc coated steel’s corrosion resistance may be inferior to that of stainless steel.
3. Mechanical Properties
When it comes to physical properties, stainless steel generally offers higher strength, hardness, and toughness compared to aluzinc coated steel. It also maintains its structural integrity at high temperatures, making it suitable for use in high-heat and high-pressure environments, such as in food processing equipment, medical devices, and industrial machinery.
Aluzinc coated steel, while having lower tensile strength than stainless steel, is easier to form and process. It can be easily stamped, bent, and cut, making it ideal for use in applications where complex shapes are needed, such as in roofing, wall cladding, and ventilation ducts. Its excellent formability allows for the production of lightweight yet durable components, especially in construction and architectural applications.
4. Cost Considerations
Cost is a significant factor when choosing between aluzinc coated steel and stainless steel. Stainless steel, due to its high alloy content, has a higher raw material and processing cost, particularly for grades like 316 stainless steel that contain significant amounts of nickel. The cost of stainless steel can be prohibitive in large-scale or cost-sensitive applications.
In contrast, aluzinc coated steel is more cost-effective. The production process for aluzinc steel is relatively simple and inexpensive, and the materials used for the coating (aluminum, zinc, and silicon) are more affordable than the high-grade alloys found in stainless steel. This makes aluzinc coated steel a more economical choice for large-scale applications, particularly where corrosion resistance is needed but the extreme durability of stainless steel is not required.
5. Aesthetic and Surface Finish
Aesthetically, stainless steel has a distinct advantage due to its smooth, reflective surface that can be polished to a high sheen. This makes it a popular choice for applications where the appearance is important, such as in architecture, interior design, and consumer goods. Stainless steel can also be textured or brushed for decorative effects.
Aluzinc coated steel, on the other hand, has a more utilitarian appearance. Its surface is typically matte with a silver-gray finish, although it can be treated with various coatings to improve its appearance. While it may not have the same polished shine as stainless steel, it can still blend well in modern architectural designs, particularly in industrial and construction applications.
Conclusion
Both aluzinc coated steel and stainless steel offer excellent corrosion resistance and durability, but the choice between them depends on specific application requirements. Stainless steel is ideal for environments where high strength, heat resistance, and corrosion resistance to acids and chlorides are paramount. In contrast, aluzinc coated steel offers a cost-effective solution for general construction, roofing, and other applications where formability and moderate corrosion resistance are key.