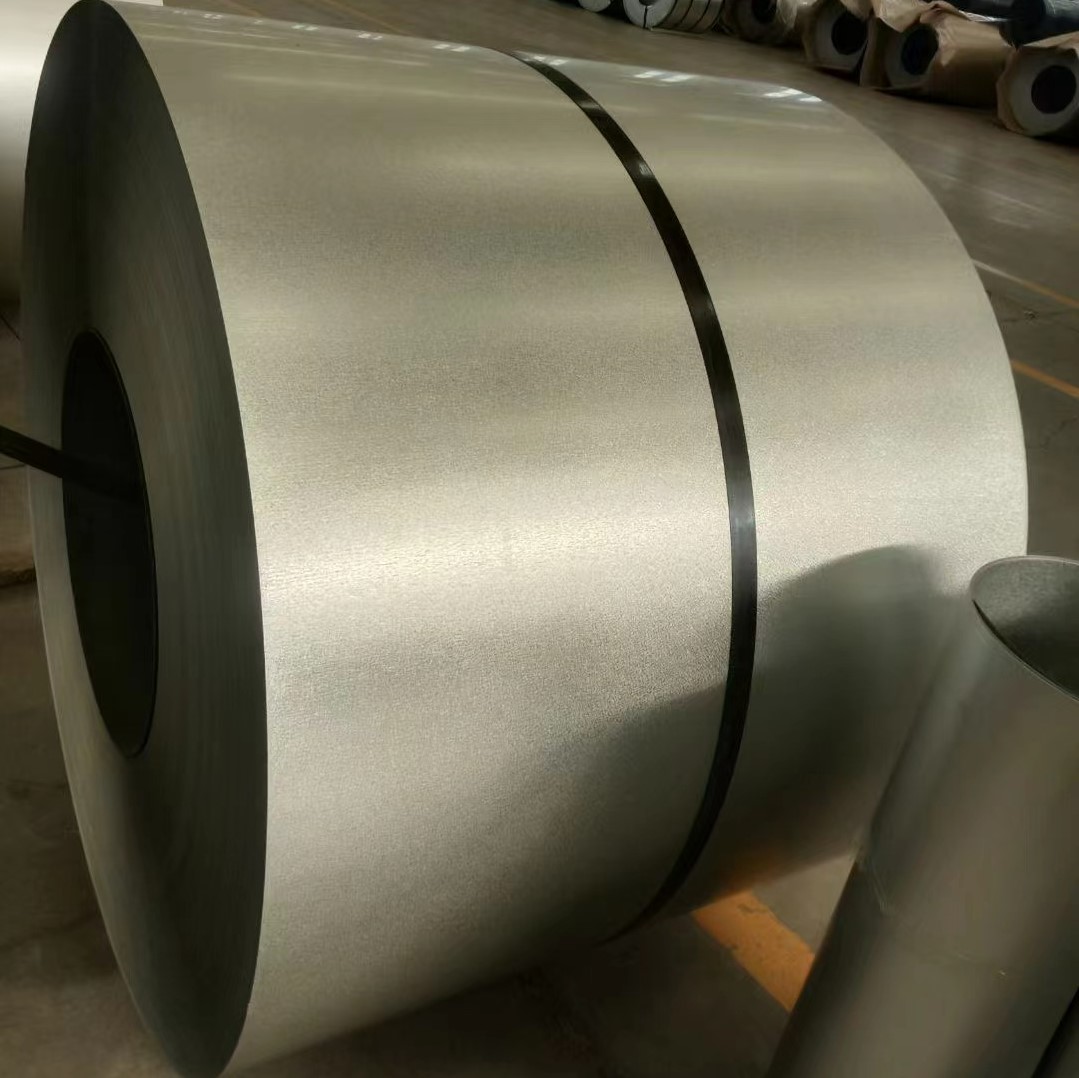
Langzoholding NEWS: Galvanized Steel – Performance Advantages, Expanding Applications, and Evolving Industry Trends
I. Core Characteristics and Manufacturing Process Innovations
Galvanized steel stands as a cornerstone of modern industrial materials, renowned for its exceptional corrosion resistance and durability. The manufacturing process involves coating steel with a protective layer of zinc, achieved through two primary methods:
- Hot-Dip Galvanized Steel – This method submerges steel in molten zinc, creating a robust coating (30-200μm) ideal for harsh environments. It is widely used in construction (structural beams, transmission towers, highway guardrails), agriculture (silos, fencing), and marine applications (bridges, offshore platforms).
- Electro-Galvanized Steel – Utilizing an electrochemical process, this technique deposits a thinner zinc layer (3-20μm), ensuring a smoother surface finish. It is preferred in automotive manufacturing (body panels, chassis components), home appliances (refrigerators, washing machines), and electronics (server racks, enclosures).
The Chinese galvanized steel market continues to dominate global production, with 2024 output projected to exceed 60 million metric tons, accounting for over 45% of the world’s cold-rolled steel supply (China Iron and Steel Association). This growth is fueled by rising infrastructure investments, automotive demand, and renewable energy expansion.
II. Cutting-Edge Technological Developments Enhancing Performance
Recent advancements in galvanized steel production have significantly improved its mechanical properties and environmental sustainability:
1. Advanced High-Strength Formulations
- Baowu Group’s 1200MPa-grade galvanized steel is a breakthrough for the electric vehicle (EV) industry, enabling 15% weight reduction in battery enclosures while maintaining crash safety and corrosion resistance.
- Dual-phase galvanized steel (DP-GI) is gaining traction in automotive manufacturing, offering superior formability and strength for lightweight vehicle designs.
2. Environmental Process Improvements
- Shougang Jingtang’s chromium-free passivation technology eliminates toxic hexavalent chromium, reducing heavy metal emissions by 90% and complying with EU REACH regulations.
- Water-based pre-treatment coatings are replacing solvent-based systems, cutting VOC emissions by 30% while enhancing coating adhesion.
3. AI-Driven Quality Control
- Ansteel’s AI-powered visual inspection uses deep learning algorithms to detect microscopic defects with 99.2% accuracy, reducing material waste and improving production efficiency.
- Real-time zinc coating thickness monitoring ensures consistent quality, minimizing deviations in corrosion protection performance.
III. Expanding Application Markets and Demand Dynamics
The versatility of galvanized steel continues to drive adoption across multiple industries:
Sector | Primary Applications | Market Growth Trends | Key Demand Drivers |
---|---|---|---|
Construction | Structural framing, roofing, facades | 6.5% annual growth | Urbanization, green building codes |
Automotive | Body panels, chassis, EV components | 8.7% annual increase | Lightweighting, fuel efficiency |
Consumer Goods | Appliances, electronics, furniture | 4.2% yearly expansion | Durability, aesthetic appeal |
Renewable Energy | Solar mounting, wind turbine towers | 12.3% rapid growth | Global shift to clean energy |
Solar energy applications are a major growth area, with galvanized steel being the preferred material for PV mounting structures due to its weather resistance and structural integrity.
IV. Evolving Global Trade Policies and Compliance Requirements
The galvanized steel industry faces new regulatory challenges:
1. European Union (CBAM & REACH Compliance)
- The Carbon Border Adjustment Mechanism (CBAM) requires detailed carbon footprint documentation for imports, increasing compliance costs for Chinese manufacturers.
- ISO 14025 Environmental Product Declarations (EPDs) are now mandatory for EU-bound shipments, ensuring adherence to sustainability standards.
2. North America (ASTM & AISI Standards)
- The updated ASTM A123-24 specification raises zinc coating adhesion requirements by 20%, pushing manufacturers to refine their galvanizing processes.
- AISI’s new corrosion testing protocols demand longer salt spray resistance (1,000+ hours), particularly for automotive and construction-grade galvanized steel.
3. Asia-Pacific (Green Manufacturing Initiatives)
- China’s “Dual Carbon” policy is accelerating the adoption of low-emission galvanizing technologies, including hydrogen-based reduction methods.
- India’s PLI (Production-Linked Incentive) scheme is boosting domestic galvanized steel production for infrastructure and automotive sectors.
V. Future Outlook: Smart Coatings and Sustainable Innovations
The next generation of galvanized steel will integrate:
- Self-healing zinc coatings – Microcapsule-based repair mechanisms to extend product lifespan.
- Nano-coated galvanized steel – Enhanced corrosion resistance for marine and aerospace applications.
- Hydrogen-reduced galvanizing – Cutting carbon emissions by 50% compared to traditional methods.
As global demand for durable, eco-friendly materials grows, galvanized steel remains indispensable across industries, driven by technological innovation and evolving regulatory standards.
Langzoholding Analysis – With rising infrastructure investments, automotive electrification, and renewable energy expansion, the galvanized steel market is poised for sustained growth, reinforcing its status as a foundational material for modern industry.